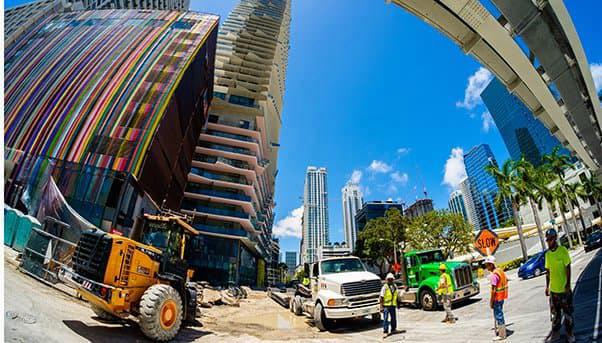
Change is slowly coming to the construction industry.
The latest occurrence came on July 3 when Caterpillar Inc announced a memorandum of understanding with Fastbrick Robotics Ltd, an Australian company whose robotics system can lay bricks better and faster than any human.
Caterpillar, the U.S. manufacturer of construction equipment, agreed to invest $2 million in the company and help develop, make and sell its systems.
Although it is a small step for the industry, it is the latest in a series being taken towards a wider use of innovative technology that could unleash the industry’s full potential. This is significant because construction has been slower than other industries in adopting new ways to improve productivity. «As a result, efficiency gains have been meagre,» according to 2016 report on the industry by the World Economic Forum.
If it eventually manages to close this productivity gap with industries like retail or manufacturing, the economic benefits would be enormous, according to “Reinventing Construction: A Route to Higher Productivity”, a study published in February 2017 by McKinsey Global Institute of the consulting firm of the same name. «It would add $1.6 trillion in value every year,» reads the study. «That would meet about half of the world’s annual infrastructure needs or boost global GDP (gross domestic product) by 2 percent.»
This estimate is huge because construction is one of the largest sectors in the global economy. Spending on activities related to construction – whether it be roads, buildings or industrial installations - accounts for 13% of the world’s GDP, or $10 trillion. And it is set to increase as demand keeps rising, especially in Asia. By 2025, spending will likely reach $14 trillion, the study says.
Construction has enormous potential to produce value because it has been slower to innovate than other industries. Its labor-productivity growth has averaged 1% a year during the last two decades against 2.8% for the world economy and 3.6% for manufacturing, according to the study.
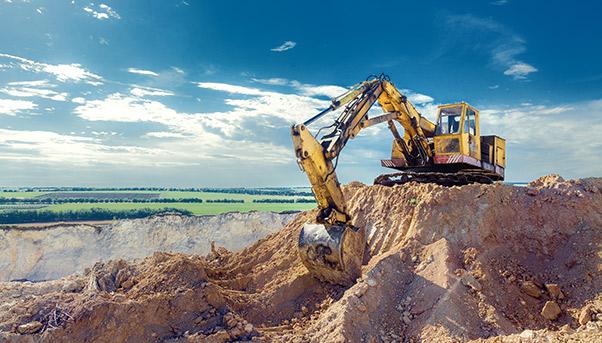
The reasons are many, such as a lack of investment in research and development.
This leaves plenty of room for improvement, and the McKinsey study cites a number of areas where it could be done, explaining how productivity could increase by 50-60% as a result.
One of those areas is digital technology, which includes robotics. Companies in the United States and Australia have been testing offerings from Fastbrick Robotics and others for repetitive jobs like brick-laying and have discovered how they have been able to increase masonry productivity gains by more than 10%, according to the study.
Drones are being deployed on construction sites for safety and maintenance inspections. Sensors – some worn by workers – help track productivity.
Then there are new materials and three- and five-dimensional modelling. But process, a seemingly mundane area compared with these technological innovations, can be just as effective, especially in design and engineering.
The McKinsey study suggests treating construction as a production system. By using more common parts, the cost of supplies can go down and the time needed to put up a building, for example, can quicken. «If construction were to depart from entirely project-based approaches to more consistently employ a manufacturing-like system of mass production with much more standardization and manufacturing of modules and parts in factories off-site, the productivity boost (by five to ten times) could be an order of magnitude greater,» it says. It gives the example of a U.S. company whose production system enables it to reduce on-site craft work by 85% and bring unit cost to 35% below the market rate. «Dramatic time and cost savings …add up to much higher productivity,» it says.
But companies cannot do everything by themselves. They also need help from the public sector. The report by the World Economic Forum urges authorities to simplify and harmonise building codes and standards to make it easier for builders do to their jobs. «By setting and enforcing time limits for construction permits and environmental approvals, governments can greatly reduce project delays,» it says, citing but a few of the permits builders need before beginning their work.